Revolutionizing Manufacturing for Small Businesses
Small plastic Injection molding machine has long been one of the most efficient and widely used methods for producing plastic parts in high volumes. However, traditional large-scale injection molding machines are often too costly and too big for smaller businesses, startups, or specialized industries. Enter the small plastic injection molding machine: a more affordable, compact, and efficient solution for small-scale production. In this blog, we will explore the features, advantages, applications, and key considerations when investing in a small plastic injection molding machine.
How to Use this Machine
A small plastic product injection molding machine is a key piece of equipment used in the manufacturing of plastic parts and products across various industries. The machine operates by melting plastic pellets and injecting the molten plastic into a mold under high pressure. Once the plastic cools and solidifies within the mold, it takes the desired shape and can be ejected as a finished product. This process is widely used to produce a wide range of plastic items, from simple components to intricate, multi-part assemblies.
How It Works
The small plastic injection molding machine process begins by loading plastic pellets into the hopper of the injection molding machine. The pellets are then heated in the barrel, where a rotating screw melts them into a molten state. Once the plastic reaches the desired temperature, it is injected into a mold under high pressure, filling every cavity. After cooling, the mold is opened, and the finished part is ejected.
What is a Small Plastic Injection Molding Machine?
A small plastic injection molding machine works based on the same principles as a traditional injection molding machine, but on a smaller and more affordable scale. These machines melt plastic pellets and inject the molten material into a mold under high pressure. While larger injection molding machines are designed to handle high-volume production, small machines are perfect for low to medium-volume runs, prototyping, and customized plastic parts.
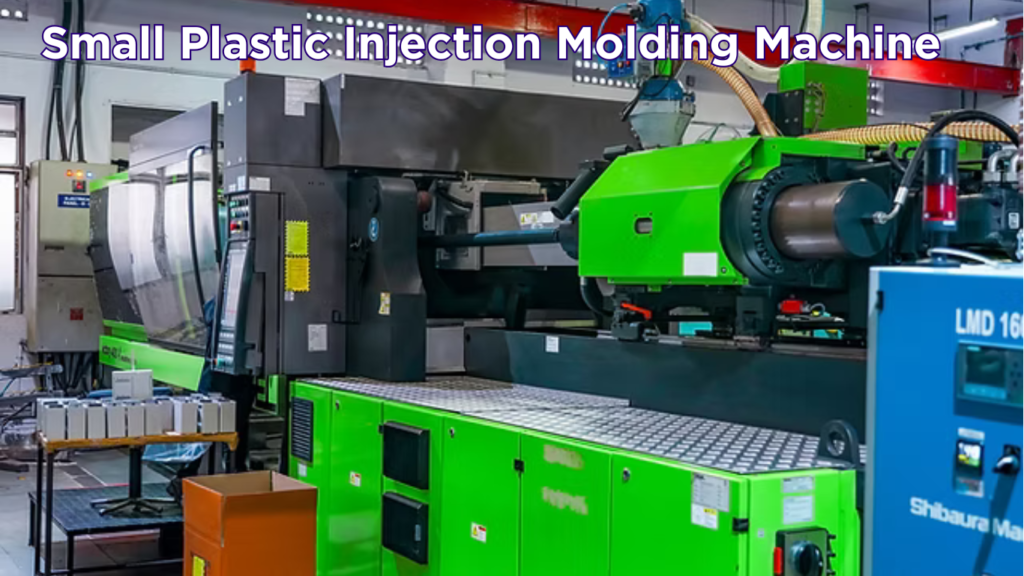
Key Components of a Compact plastic injection molding machines
Even though they are compact, Compact plastic injection molding machines contain the same essential components as their larger counterparts. These include:
- Injection Unit: The part of the machine where plastic is melted and injected into the mold.
- Screw and Barrel: Used to melt the plastic before injecting it.
- Heating Elements: Ensure the plastic reaches the desired temperature for injection.
- Clamping Unit: Holds the mold in place during injection to ensure the mold stays tightly closed. This unit generates the required clamping force for successful molding.
- Hydraulic/Electrical Systems: These systems power the injection and clamping units. Small machines may have an integrated hydraulic and electrical system for improved energy efficiency.
- Control System: The interface that operators use to adjust machine settings, monitor performance, and manage the injection process.
Key Features and Benefits of Small Plastic Injection Molding Machines
1. Compact and Space-Saving Design
One of the most obvious advantages of small plastic injection molding machines is their compact size. Unlike large machines, which require significant floor space, small machines can fit into smaller work areas, making them ideal for businesses with limited space. These machines are perfect for workshops, labs, or production facilities that need to maximize available space.
2. Affordable and Cost-Effective
Traditional industrial injection molding machines can cost hundreds of thousands of dollars, making them out of reach for many small businesses. Small plastic injection molding machines are far more affordable, often costing a fraction of the price of larger machines. This makes them an excellent choice for startups, small manufacturers, or anyone wanting to enter the injection molding space without committing a large amount of capital.
Beyond the initial cost savings, small machines are also more cost-effective in the long run due to their lower energy consumption and reduced maintenance requirements.
3. Precision and High-Quality Production
While small in size, these machines can produce high-precision plastic parts. Small plastic injection molding machines are ideal for manufacturing small, intricate components that require high levels of accuracy. Whether you need parts for consumer goods, automotive components, medical devices, or electronics, these machines can deliver high-quality results.
The precision capabilities of small machines make them perfect for industries where product quality and consistency are essential. Furthermore, they often come equipped with advanced controls that allow operators to fine-tune the molding process for optimal results.
4. Versatility in Materials and Applications
Small plastic injection molding machines are versatile in terms of the materials they can process. These machines can handle a wide range of thermoplastics, including:
- ABS (Acrylonitrile Butadiene Styrene)
- Polycarbonate (PC)
- Polypropylene (PP)
- Nylon (PA)
- Polystyrene (PS)
This variety of materials allows small manufacturers to create a broad range of products for different industries. Whether you need a strong, heat-resistant material for automotive parts or a lightweight, flexible material for consumer goods, small plastic injection molding machines can accommodate your needs.
5. Ease of Use and Maintenance
Another benefit of small plastic injection molding machines is their user-friendly design. Modern machines come with digital control interfaces, touchscreens, and automated features, making it easier for operators to set up and run production cycles. This ease of use minimizes the learning curve for new operators and helps maintain consistent production quality. https://www.facebook.com/reel/1852653242173031
Additionally, small machines require less maintenance compared to larger counterparts. The simpler design and smaller components make routine maintenance tasks—such as cleaning and lubrication—more manageable, resulting in fewer machine downtimes and a lower total cost of ownership.
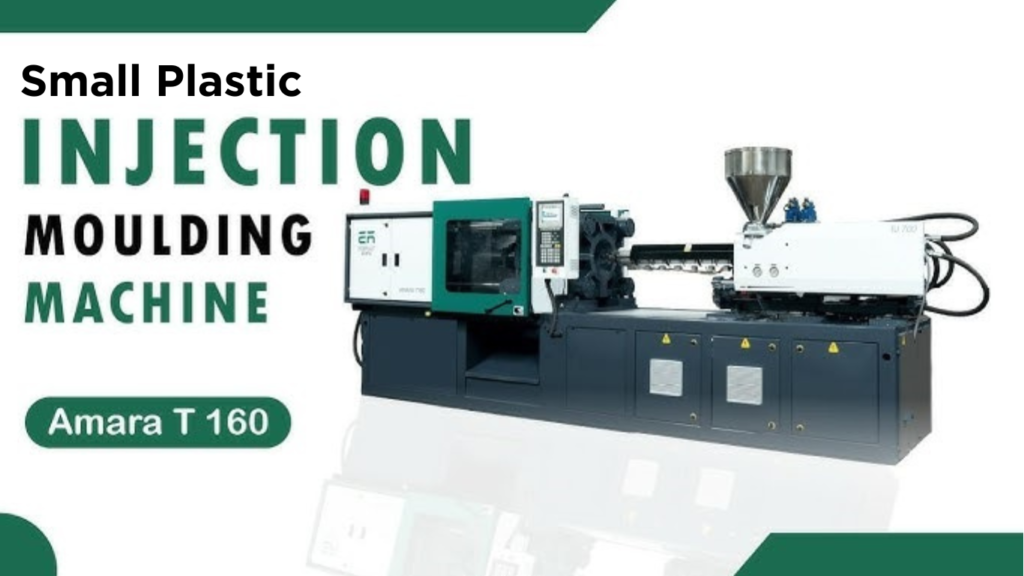
Applications of Small-scale injection molding machines
1. Prototyping and Product Development
Small-scale injection molding machines are ideal for prototyping and product development. When designing a new plastic part, companies often need to create small batches for testing and iteration. Small machines allow engineers and designers to quickly produce prototypes to evaluate functionality, design, and fit. This reduces the time spent on product development and helps bring products to market faster.
2. Small-Batch Production
For manufacturers that do not require mass production, small plastic injection molding machines are the perfect solution for small-batch production. Whether you’re producing limited quantities of parts for niche markets or testing new designs, small machines can efficiently handle small production runs. Industries such as medical devices, automotive, and consumer goods frequently rely on small-scale production for custom parts or specialty items.
3. Educational and Training Purposes
Many educational institutions use small plastic injection molding machines for teaching purposes. These machines provide students with hands-on experience in the injection molding process, helping them understand the technology and its application in manufacturing. Small machines are especially useful in training environments where space is limited, or where students need to learn on a smaller scale before advancing to larger equipment.
4. Customized and Specialized Parts
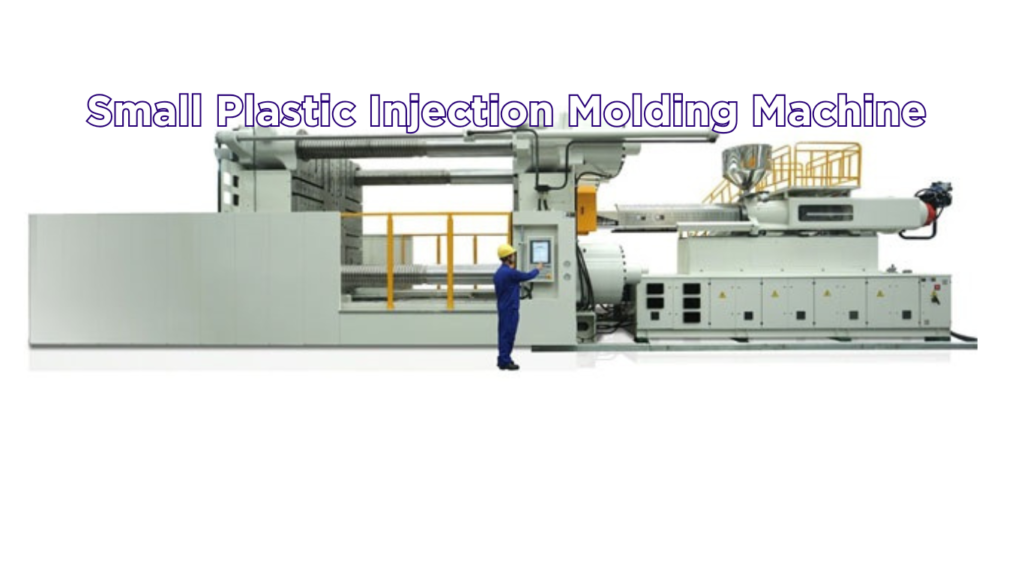
How to Choose the Right Small Plastic Injection Molding Machine
1. Assess Your Production Needs
The first step in choosing a small plastic injection molding machine is understanding your production requirements. Consider factors such as:
- Production Volume: Are you looking for a machine that can handle small runs or one that can scale up to moderate production volumes?
- Part Complexity: What is the complexity of the parts you plan to produce? Some machines are better suited for simple components, while others can handle more intricate designs.
- Material Compatibility: Ensure the machine you choose can process the types of plastics you need for your specific application.
2. Evaluate Key Specifications
When evaluating small injection molding machines, it’s important to consider the following specifications:
- Clamping Force: This is the amount of force the machine can apply to keep the mold closed during injection. Choose a machine with sufficient clamping force for your part size and material.
- Shot Size: The shot size refers to the amount of plastic the machine can inject into the mold. Make sure the shot size is suitable for the parts you intend to produce.
- Injection Speed and Pressure: Machines with adjustable injection speeds and pressures provide more control over the molding process, ensuring high-quality production.
3. Consider Machine Size and Space Requirements
Although small injection molding machines are compact, it’s still important to ensure the machine fits within your available production space. Measure the space where the machine will be placed and ensure there is enough room for proper operation and maintenance.
4. Budget and Total Cost of Ownership
Small plastic injection molding machines are more affordable than larger machines, but it’s still essential to consider the total cost of ownership. Factor in the initial cost of the machine, as well as ongoing costs such as maintenance, energy consumption, and potential repairs. This will help you assess the true value of the machine and determine if it fits within your budget.
Maintenance and Troubleshooting Tips for Small-volume injection molding machines
1. Regular Cleaning and Lubrication
Routine cleaning and lubrication are essential for keeping your small plastic injection molding machine in optimal working condition. Clean the mold cavities regularly to avoid contamination, and lubricate moving parts to prevent wear. https://esemplastavinya.com/injection-molding-machine/
2. Troubleshooting Common Issues
Common problems such as short shots (incomplete filling of the mold), flashing (excess material around the part), and mold wear can be resolved with proper maintenance. Regularly inspect the machine’s components and perform calibrations to ensure consistent performance.
3. Preventive Maintenance
Invest in a preventive maintenance plan to avoid major issues and reduce downtime. This should include regular checks of the hydraulic and electrical systems, as well as monitoring the injection unit and clamping system for wear and tear.
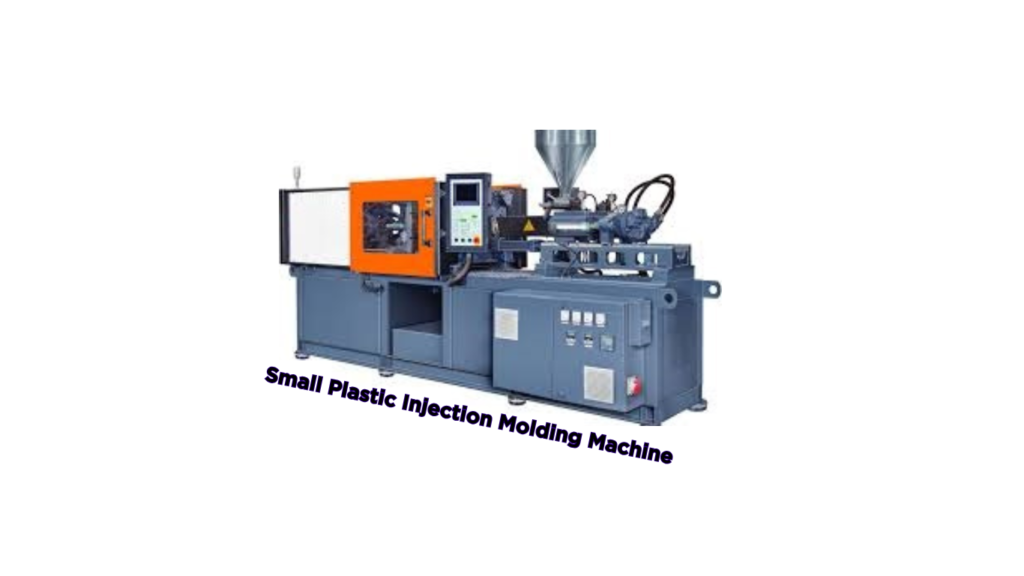
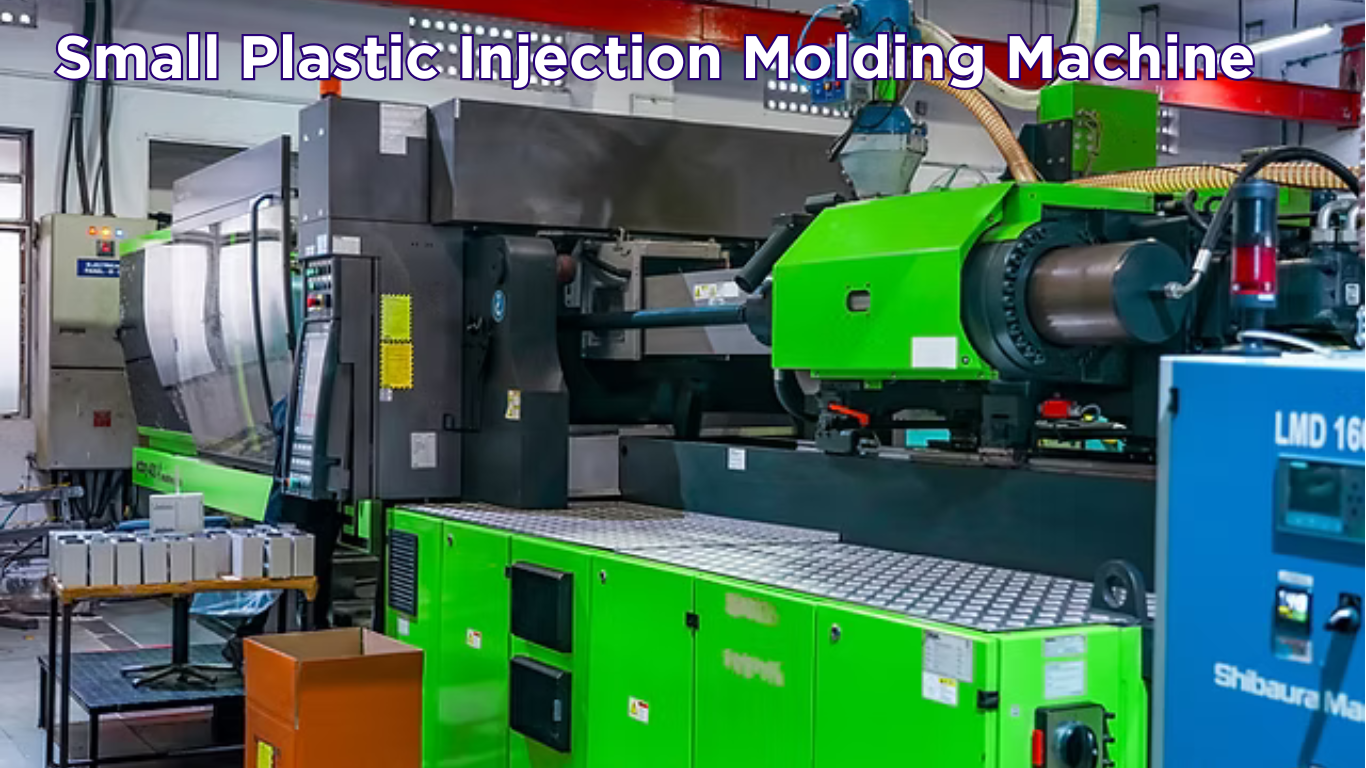
Conclusion
Small plastic injection molding machines have become a game-changer for small businesses, startups, and manufacturers seeking cost-effective, space-efficient, and high-precision production solutions. These machines offer an affordable entry point into the world of injection molding while delivering the flexibility and performance required to produce high-quality plastic parts. By understanding their features, benefits, and applications, businesses can make informed decisions about incorporating small plastic injection molding machines into their production process. Whether for prototyping, small-batch production, or customized parts, small injection molding machines offer a wide range of opportunities to enhance productivity and reduce costs.